ユーザー様より頂いた3Dプリンタを使用した船舶ラジコンの製作記をご紹介させて頂きます。
CADも3Dプリンタも全く使った事が無かった方が、それらを活用し船舶模型を作り込まれています。
3Dプリンタの活用方法だけではなく、型紙づくりやFRP積層の方法など、とてもマニアックで大変貴重な内容ですのでぜひ最後までご覧ください。
※一部スライサー(ソフトウェア)のバージョンが古く、最新スライサーと異なる場合が御座います。
3Dプリンタを活用した船舶模型の製作
《青函連絡船タグボート ひうら丸模型製作過程》 著者:平川地 まばせ
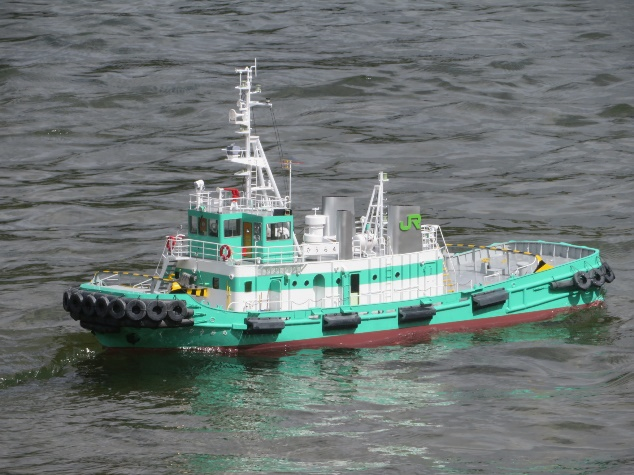
青函連絡船タグボート ひうら丸 完成模型
目次
- プロローグ
- 3Dプリンタ
- 船舶模型の製作工程
3.1作図に必要な資料の準備
3.2ハルの製作
3.2.1 型紙づくり
3.2.2 型紙で材料にケガいて切り抜き貼合わせ
3.2.3 素地調整
3.2.4 コーティング
3.2.5 離型剤処理
3.2.6 FRP積層
3.2.7 外形調整
3.2.8 切断、離型
3.2.9 ケガキ
3.2.10 穴あけ、部品取り付け
3.2.11 寸法調整、筋交い固定、甲板製作
3.2.12 水漏れ確認 - CADデータの作成
4.1 部品の寸法を確定しCADで作図する
4.2 CADからSTLファイルに出力する
番外【製作メモ1】CAD描画の時に考慮したこと - スライス
5.1 STLファイルを取り込む
5.2 サポート材を設定する
5.3 スライスの設定をする
5.4 Gコードを作る
番外【製作メモ2】スライスソフトの便利な機能 - 3Dプリンタでの造形(Adventurer3)
6.1 プリンタを準備する
6.2 3DプリンタにGコードを取り込む
6.3 ファイルを選び造形
6.4 造形終了
6.5 仕上げの前に仮組みして確認
番外【製作メモ3】造形で職人技を楽しむ - 組み立て工程
7.1 モデルの仕上げ
7.2 塗装前の組み立て
7.3 塗装
7.4 組み立て
7.5 全体の組み立て
7.6 通電確認
7.7 ウエイト調整
番外【製作メモ4】工程あれこれ - 駆動系の実装
- 進水
- 製作を振り返って
- NSS編集後記
1. プロローグ
友人より、「船の模型を作って走らせようよ」と言われ、製作に挑戦することにしました。
製作ターゲットは、青函連絡船の着岸を補助していたタグボート「ひうら丸」に決め、1/30のスケールで作ることにしました。
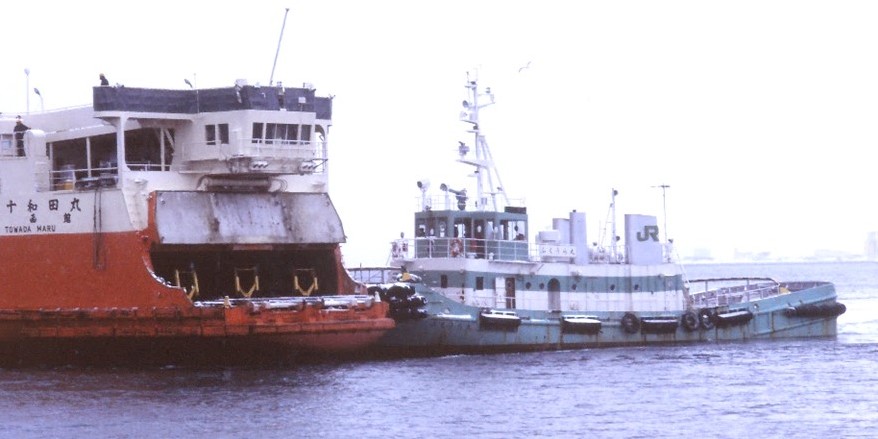
同型船のふくうら丸
最初はプラスチックの板材と真鍮の棒材で鉄道模型のように作ろうと思い、試し曲げや部品を試作したものの、大量のボルトがある後部のハッチの製作に困ってしまいました。
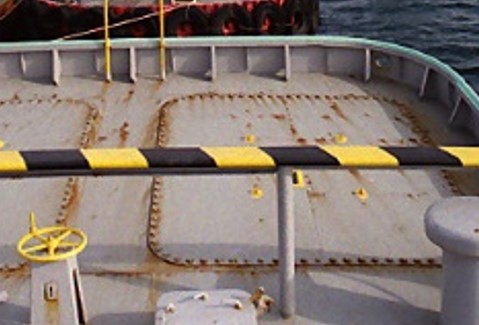
後部のハッチ部のボルト
そこで思いついたのが3Dプリンタでした。
しかし、3Dプリンタはよく聞く割に見たこともないし、量販店にも売ってない。現物を見ず、説明も受けないでインターネットで買うのはなかなかリスクがあります。
そんな中、株式会社エヌエスエスという会社が運営している3Dプリンタのショールームがあることがわかりました。
HPで見学の受付をしており、希望日を入れるとすぐ返事がきましたので予約しました。
3Dプリンタは見たこともないし、聞きたいこともたくさんあるので心強く感じました。
2. 3Dプリンタ
当日は以下のことを教えてもらおうと考えました。
【当日の質問項目】
・機種はどんなタイプがあり、どのような造形ができるのか。
・造形のための設計(CAD)はどうするのか?
・設計したらプリンタにどのようにインプット(連携)するのか?
・音や匂いはないのか。
・造形の精度とスピード、造形可能な大きさとプリンタの価格の関係。
・材料の種類と値段は?
・実際に動いているところが見たい。
・購入から造形開始までの準備や順序などの流れ。
ショールーム見学当日……
エヌエスエスさんのドアを開けると、ずらりと並んだ各種3Dプリンタが実際に動いていて、造形していました。
上記の質問項目を伺ったり、実際の造形品を見ながら製作のコツを教えていただき、質問事項はすべて解決。
購入することを決め、機種選択に入りました。
……その結果…… 「FLASHFORGE Adventurer3」(フラッシュフォージ アドベンチャー3)に決めました。
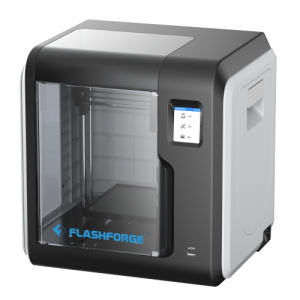
FLASHFORGE Adventurer3
Adventurer3の造形範囲は150㎜×150㎜×150㎜と小さめですが、自分の模型なので接着でつなげばよく、小型(自室に置ける)で安価ということで即決しました。(3Dプリンタ本体と、スライスソフト双方にわかりやすいマニュアルが完備されています)
実際寝室に置いて、寝ている間動作させていましたが音は静かで、においもなく、朝起きると造形が終わっていて効率よく使いこなせました。使いはじめ、不明なところはエヌエスエスさんにメールするとすぐ返答があり、とても親切にアドバイスをいただきました。
3. 船舶模型の製作工程
今回作るのは1/30スケールのタグボートで、全長101㎝あります。
ハル(船体下回りの船殻)は模型製作を勧めた友人のトワマさんに作り方を聞きながらFRPで作り、キャビンと付帯する部品は3Dプリンタで作ることにし、材質は強度、加工と塗装のしやすさ、接着強度に優れたABSにしました。甲板(床)は造形する材質と同じABSの板材を使いました。
3.1 作図に必要な資料の準備
部品を作るには確定した寸法が必要になりますので、船体や部品の図面を書くための資料を用意します。
船の総体図は「一般配置図」とよばれ、船の専門誌に載っていたりするほか、実際の船内に掲示してあります。細部は乗船して写真に収めるとよいでしょう。
今回作成する船はすでに実物の船はありませんが、写真があったことと、青函連絡船史料研究会さんからハンドブックを借用できましたので、寸法や位置の割り出しに大変役立ちました。
3.2 ハルの製作
3.2.1 型紙づくり
図面は船体の側面図、上から見た平面図の半分を、A1サイズのトレス紙に書きました。
型は、形状の変化が大きい部分は小刻みに、変化の少ない部分はまびきます。材料はバルサ材の1㎜、2㎜、3㎜と、スチロール板の5㎜、建築用断熱材(スタイロフォーム)の25㎜を使い、それに応じ図面にもその厚み分の線を入れ、あとは想像で型紙にケガキ線を入れ、切ります。型紙は左右どちらか片側だけで、ひっくり返して使うと左右対称になります。
切ったら中心線側を揃えて不自然な箇所がないか確認し、あったらやり直します。
3.2.2 型紙で材料にケガいて切り抜き貼合わせ
材料に中心線を書き型紙を当てて、まず左右どちらか片側だけケガキ線を入れ切ります。
切り取った材料の中心線をそろえ、積み重ねてみて、不自然な箇所はやり直します。
図面の上に載せ、中心線を合わせて外形を確認し、よければ反対側も切ります。
次に図面に載せて中心線を合わせ、ねじれに注意しながら全体を3~4分割にまとまるよう接着します。
3.2.3 素地調整
現在貼り合せて段差がありますので、表面をなだらかにする作業です。凹部にはパテを塗りこみます。私の場合研ぎやすい「寒冷紗(かんれいしゃ)用パテ」を使いました。
パテが乾いたら紙やすりで研ぎます。広い面積や緩やかな曲線は、板などの平面に紙やすりを貼り付けて研ぎます。
最後は図面上に載せて外形の一致を確認して一体に接着します。作業しやすいように足を付けました。
3.2.4 コーティング
離型剤を付着させるため樹脂をコーティングします。
発泡スチロール用樹脂(促進剤入り)に硬化剤を混ぜ、刷毛でFRPを施工する全体に塗布します。表面が滑らかに、ピカピカになります。
※材料はFRP-ZONE社さんのネットショップで購入しました。同社HPに素材の詳しい説明も掲載されています。
3.2.5 離型剤処理
固まってから離型剤を塗布、またはスプレーします。
3.2.6 FRP積層
使った材料はガラスクロス#200(薄手、滑面)、ガラスマット#450(厚手、中間層で使用)、ロービングクロス#580(中厚手、高強度)、FRPポリエステル樹脂(インパラ)4Kg,と硬化剤MEKPO100ccです。
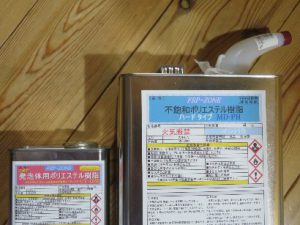
樹脂材料
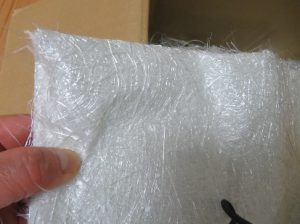
ガラスマット
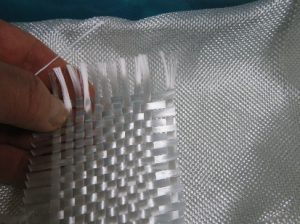
ロービングクロス(手前)とガラスクロス
作業エリア周囲を含めて樹脂が垂れてもいいように、広めに養生します。ガラス繊維が服や体につくといつまでもチクチクするので必要に応じて服や靴、肌を養生します。肌にベビーパウダーを塗布しても緩和できます。
最初の施工は型によくなじむガラスクロス#200をはさみで切り、全体に網羅するようにかぶせ(あとで凸凹を研磨するので重なってもよい)余りは下に垂らします。
樹脂に硬化剤を入れるとすぐ硬化が始まるので、ローラでたっぷり染み渡るように垂れるぐらいに塗ります。
(気泡を絶対入れないように。強度が低下するのと、補修が大変)
次にガラスマット、ロービングクロス#580、最後に再度ガラスクロス#200を施工してみました。これで約3ミリ厚ぐらいになります。
3.2.7 外形調整
型がついた状態で研磨機、手作業で表面を調整します。しっかり仕上げないと塗装した時に凸凹になります。水洗いしながら表面状態を確認して仕上げます。
型から外すと力を入れられなくなるので、型がついたまま作業します。
3.2.8 切断、離型
サンダーに樹脂用のカッターを取り付け、下に垂らした余計な部分を2㎜程度多めに残して切ります、その後慎重に手作業で規定寸法になるよう研磨します。
離型は、型とFRPの間に徐々に空気や水を入れながら、密着している面積を徐々に少なくしながら取り出しますが、FRPは内側方向に収縮していて離れにくいので、最悪型の一部を壊して取り出します。
3.2.9 ケガキ
これから多数の部品を正確な位置に取り付けるため、1cm間隔の目安線をケガきます。
水平、垂直に保った状態にして、トースカンと油性ペンでケガきます。
3.2.10 穴あけ、部品取り付け
船体に付属する部品をアルミ板などでつくります。(主に糸のこを使用)
ハルには取り付け穴をあけます。(φ3程度のドリルで複数穴あけし、ルーターや、やすりで研磨して穴をつなげる)
次に 部品を取り付け、エポキシ接着剤などで接着します。
削りかすにガラス繊維が入っているので、掃除機のノズルで吸いながら作業することをお勧めします。
アンカーのくぼみは、大きく穴をあけたうえで、エポキシパテを埋め込み成形します。左右対称なので型紙を作り、裏返して反対側にも穴をあけます。
3.2.11 寸法調整、筋交い固定、甲板製作
FRPは内側に収縮して開口部の寸法が出ていないので、筋交いをかませて既定の寸法に固定します。L字のアルミ材に、棒材を固定します。L字の材料を船体の曲線に沿って曲げるには、L字の一方をたたくと膨張して自然に曲がります。
甲板はABSの板材を加工します。長手方向は凹型に反らせるため、裏側にカッターナイフで小刻みに切り込みを入れると膨張して自然に反ります。幅方向は中央を凸型の形状にするため、形状に合わせた骨を複数接着して目的の形状にします。
3.2.12 水漏れ確認
ウエイトを入れて水漏れがないか確認します。
どの程度のウエイトが必要かも把握できます。
4.CADデータの作成
ここからCADと3Dプリンタでの造形に入ります。3Dプリンタで造形するためは、
① CADで作図し(☞4.1)、STLファイルを作る(☞4.2)
② 3Dプリンタ付属のスライスソフトにSTLファイルを取り込む(☞5.1)
③ スライスソフトで造形に必要な設定を行いGコードを作る(☞5.4)
④ 3DプリンタにGコードを取り込む(☞6.2)
これで造形が可能になります。
4.1 部品の寸法を確定しCADで作図する
CADに寸法入力するために、あらかじめ部品の寸法を確定したポンチ絵を作っておくと便利です。実物の寸法がわからないものは写真を参考に組立図を書いてみて、各部品の寸法をある程度予測で割り出します。
以下はウインドラス(揚錨機)のAssyで、写真を見ながら図面にしました。
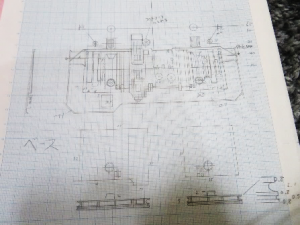
①組み立て図を書いて
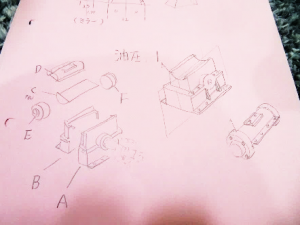
②分解図で子部品を検討し
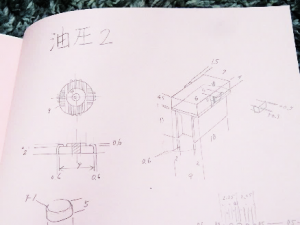
③子部品ごとに寸法確定
角度がついた部材同士交差するような計算困難な部品は、基準寸法や角度をメモに書いておき、CADで組立図を描きながら押出して交差させたり、修正や切取りを組み合わせて描画しながら部品にすると簡単にできます。
4.2 CADからSTLファイルに出力する
CADの機能でSTLファイルに出力します。右の画像はPCのエクスプローラですが、STLファイルとそれを取り込んでCADのスライスソフトで作成したGコードを管理しています。
私の場合は似ている部品が多いので使用部位ごとにフォルダーを作って分類するほか、設計変更や廃止した部品は間違い防止のため「ボツ」フォルダーに速やかに移動しています。
【製作メモ1】CAD描画の時に考慮したこと
CADの工程では、ポンチ絵を図面化(STLファイル化)するだけでなく、3Dプリンタでの造形や、最終的に仕上げや組み立てを見越して工夫することで後工程が楽に、また美しい仕上げにすることができます。
今回の模型製作でSTLファイル作成時点で工夫したことを紹介します。
◆ミラー機能で両面を美しく◆
写真のように3Dプリンタのノズル側の面は平滑で、底面は荒れた状態になります。
対称形状で両面きれいに仕上げたい場合は、CADのミラー機能で対称に分割し、造形後仕上げて貼り合せます。
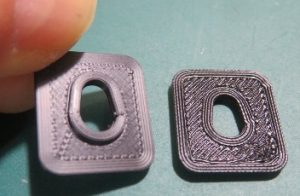
左:ノズル側 右:底面
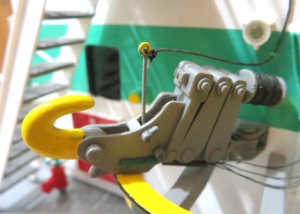
フック部品
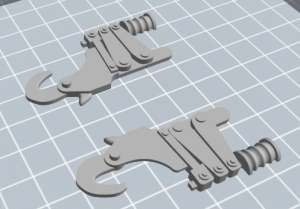
ミラーにしたところ
◆スライスに合わせてSTLファイルを分ける◆
写真は操縦スタンドですが、上面と前面を無垢で精緻(100%、スライス0.1㎜積層ピッチ)に仕上げる必要がありました。反面、本体は体積が大きく樹脂を節約するためスカスカ(密度40%、スライス0.15㎜積層ピッチ)でよいのですが、同時に造形できないため、CADの段階で別のSTLファイルにしています。
◆表裏逆にすることも◆
扉は厚みが薄く、表裏目に触れるので、あえて複雑な裏側をノズル側の面にして、表側にパテを盛って仕上げることにしました。
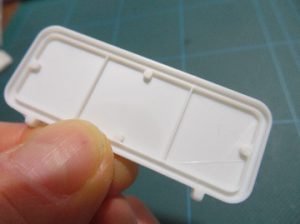
裏側を仕上げ面に
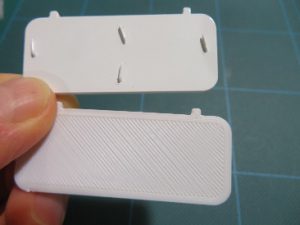
下:造形状態 上:完成品
◆捨て代で失敗を防ぐ◆
細く接地面積が少ない部品は、造形中の熱の変化やノズルがこするときの負荷でベースから浮いたりはがれたりすることがあります。(一度浮くと造形を続けても変形してしまい失敗に終わるので、早く止めて原因を考えます)
捨て代を設けて失敗を防ぎました。
◆長めに作ってカットする◆
細い部分の終端は、ノズルが折り返すためボテッと違和感のある仕上がりになります。こんな時は長めにしておいて、造形した後にカットします。
◆効率化を考えて作図する◆
写真は失敗例ですが、複数の部品を配置するときに余裕をとりすぎたので、造形に時間がかかりフィラメントにも無駄が生じました。CADの作図段階で詰めて配置するのが有用です。
◆わざと浮かせてきれいにはがす◆
写真は手すりを造形したものです。
横棒は上がφ1.8、下2本がφ1.2ですが、造形後φ1.8の部分がベースからはがれにくく壊れました。しかしφ1.2の部分は簡単にはがれました。違いはベースから浮いていたことです。全体を0.3㎜浮かせてみたところ、下の写真のようにすべてがサポート上に造形されるので簡単にはがれ、成功しました。
3Dプリンタにファイルを取り込んだときに浮かせることもできますが、再製作も考慮し作図段階で浮かせたほうが無難です。
◆文字やロゴは写真を利用する◆
CADに写真を取り込んで、なぞって描画します。
取り込む写真は、真正面からひずみなく撮影されていれば修正不要ですが、必要ならフォトショップなどの画像編集ソフトで縦横比や角度の修正をしておきます。
造形は文字の部分を0.5㎜程度の凹か凸にして、後で油性ペンで塗ります。
↑実物写真
↓本模型
◆組み立てを考慮する◆
手すりのタテの筋交いは細い板(帯板)なので、断面は細い長方形です。手作業で角穴はあけられないので、根元を2φの円形にすることで、2φの穴をあけて差し込めるようにしてあります
5. スライス
CADで作ったSTLファイルをスライスソフトに取り込み、各種設定を行なって、3Dプリンタで使用するGコードに出力する工程です。
5.1 STLファイルを取り込む
スライスソフトを立ち上げ、取り込むコマンド(ロード)でエクスプローラからSTLファイルを選ぶと、造形可能スペースの枠の中に、選んだファイルの形状が表示されます。
見る方向も自由に変えられます。
5.2 サポート材を設定する
空中に浮く部分など、ノズルからの樹脂が垂れる部分はサポート材で受け止める必要があるため、この設定をします。
多彩な設定ができますが、自動設定できます。サポート材の部分が違う色で表示されます。必要ない場合はそのままスライスに進みます。
5.3 スライスの設定をする
スライスでは、解像度、壁や枠の有無、スライスの厚み、表面からの無垢の層の数、内部の充填率と内部形状、ノズルが走行するスピードなどを設定します。
5.4 Gコードを作る
以上の設定終了後、ファイル名を付けて保存すると、最終の出来栄え形状が表示され、Gコードへの出力が完了します。
【製作メモ2】スライスソフトの便利な機能
◆「ベースに載せる」機能◆
CADで高さ方向0の基準面にないまま保存したSTLファイルの造形対象や、スライスソフトで位置を変更して0点に無い場合に自動でベース基準面に設置させることができます。
◆位置を調整◆
Adventurer3のビルドボード(造形物のベース板)は表面に樹脂版が接着されていて、繰り返しの使用で徐々に膨張します。 STLファイルを取り込むと中央に配置されますが、位置を調整して1か所への集中をなくし、ビルドボードを長持ちさせることができます。
◆複数同居◆
複数のSTLファイルを取り込み、1回で複数のファイル分造形することができます。
写真のように、まずビルドボード上にベースとなる面が広めに造形され、その上に目的の造形物が印刷されるので、まとめて造形すればベースの樹脂(フィラメント)と時間が節約できます。
ただしスライスが同一設定のものにします。
◆角度変更◆
平面(XY)方向と高さ(Z)方向で強度が違うので強度調整、表面の肌の仕上がり調整などで角度を変えることができます。
XYZ各方向の数値入力、または画面を見ながら手動で設定できます。
◆スケール調整◆
取り込んだSTLファイルはCADで設計通りの100%のスケールとなりますが、変更することができます。
XYZ方向同一比率、またはそれぞれの方向別に数値を入れて設定できます。
下記写真はエキスパンドメタルを造形したものですが、サイズ違いの物を作るときに便利です。
◆分割◆
取り込んだSTLファイルの造形物を任意の位置で分割することができます。
分割して不要な方を削除できますので、特定の物だけ再製作するときに便利です。
↑分割前
↓分割して片方を削除
6. 3Dプリンタでの造形(Adventurer3)
6.1 プリンタを準備する
フィラメント、ビルドボードをセットして印刷可能な状態にします。
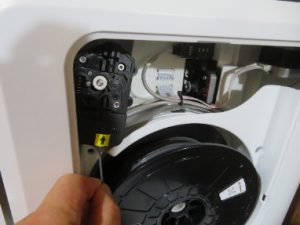
フィラメント装着
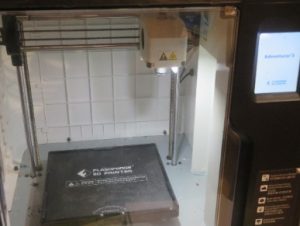
ビルドボードをセット
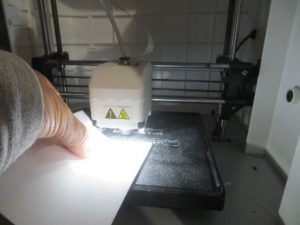
ゼロ点調整
Adventurer3ヘッド距離校正方法URL:https://nssngt.com/2018/09/12/532/
6.2 3DプリンタにGコードを取り込む
プリンターにGコードを取り込みます。WiFiやイーサネット経由もありますが、USBも可能です。
6.3 ファイルを選び造形
プリンタの画面(タッチパネル)にファイル名と立体画像が表示されるので、選択し、造形を開始します。
6.4 造形終了
Adventurer3のビルドボードは反発性があり曲げることができるので、ラフトごと簡単に外せます。さらにモデルをラフトから外せば終了です。
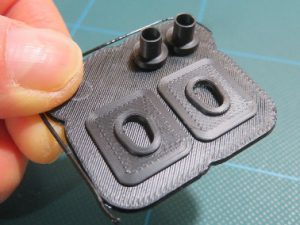
ラフト上に印刷された部品
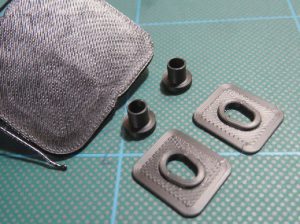
ラフトから外した部品
6.5 仕上げの前に仮組みして確認
複数の部品を接着などする前に、特にAssyは必要部品を所定の箇所に配置して寸法間違えしていないか、確認することをお勧めします。図面の上に載せたり、写真と見比べて違和感がないか、仕上げや接着前に確認します。
今回の製作ではいくつかの部品は大きすぎ組み立てできないことがありましたが、3Dプリンタのスライスソフトで任意の%で拡大縮小ができるので、すぐ再製作できました。
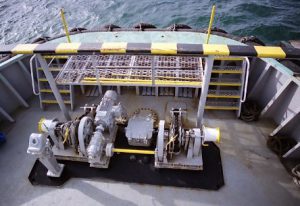
実物写真
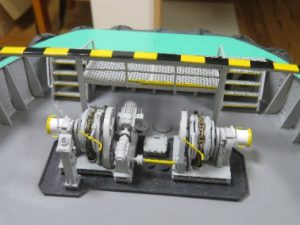
本模型
【製作メモ3】造形で職人技を楽しむ
3Dプリンターはデジタルだから、指示通り造形できると思ったら大間違い。
設定次第で出来栄えが違ってきます。初回の造形がうまくできた時は達成感があり、職人気分を味わうことができました。
以下に造形で工夫した点を紹介します。
◆スライスの設定内容を記録する◆
GXファイルを作成するときに、部品ごとに設定内容を記録し、成功したらその設定でOKとし、失敗したら成功するまで設定を変えてトライします。そうすると、形状や体積、面積などの特徴ごとに成功するパターンがわかってきますので失敗が減ります。
◆照明器具を作る◆
透明のフィラメントでLEDの光がちょうどよく拡散するレンズが作れます。まず造形後の内寸と外寸の誤差を把握して使用するLEDがぴったり入り、さらにレンズがホルダにぴったり入るように設計します。舷灯はレンズに透明グリーン、透明レッド塗料を塗ります。
右写真の投光器は、造形したホルダにLEDをはめ込み、後部でエナメル線をはんだ付けして塗装します。
◆治具を造形して金属を加工◆
網でできている「ひしがた形象物」は、3Dプリンタで円錐形の治具を作り、銅の金網を少しずつ押し付けて裾をカット。2個作り双方つき合わせてはんだ付けし、黒くスプレー塗装します。
◆その他◆
写真はフランジ継手上に8本のボルトを造形していますが、ボルトは小さく取れやすいため、造形後接着剤でコーティングすることで防止できます。
ほうきなどの小物は骨を造形し、ペンキ用の刷毛を利用して毛を接着するなど、工夫することでいろいろな造形が楽しめます。
◆失敗例◆
〈フィラメントの色も重要〉
キャビンの樹脂は、塗装色を考慮して当初白いフィラメントを使いましたが、電照のLEDを点灯させると面全体から光が透けて漏れ、黒く塗装しても完全に光の漏れを抑えることができなかったため、黒いフィラメントで造形し直しました。
7. 組み立て工程
7.1 モデルの仕上げ
造形したモデルの処置は以下に分類されます。
・仕上げしないでそのまま使う
・素地を削って仕上げる
・凹部にパテを盛って仕上げる
削る場合は写真のようにカッターナイフの刃を折ってスクレーパーとして使ったり、木片にサンドペーパーを貼って行いました。パテを盛る場合は、研ぎ性能と塗装のしやすさから、エポキシパテを使いました。
形状によっては接着してから仕上げたり、ベースについたまま仕上げることもあります。
7.2 塗装前の組み立て
Assyなど、組立て後に塗装するものは組み立てておきます。特に造形が進むにつれ部品点数が多くなるので、取り違えも防止できます。
また、3Dプリンタで造形しない甲板などの部品も並行して製作を進めます。
7.3 塗装
塗装する部品は、刷毛塗りとスプレー塗りに分け、さらに色別に分けておきます。
(スプレー塗り)
小さく軽い部品は弓のこの枠に貼ったマスキングテープに付着させ、重たいものは木片に両面テープを貼り、付着させて吹き付けます。
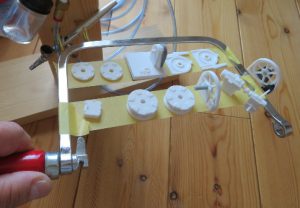
歯を外した弓のこを利用
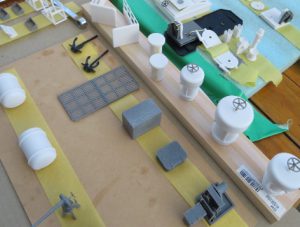
木に両面テープ貼り付け
キャビンは組み立ててしまうと形状が不安定になるので、側面ごとに塗装し、組立て後に再度接着部分を塗装します。カブリが悪い場合は塗り重ねます。
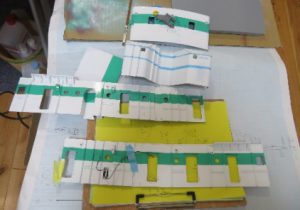
①側面ごとに塗装して
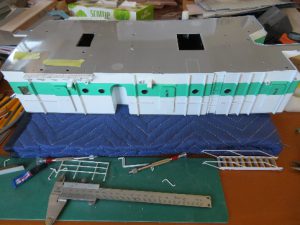
②組立て後接着部分を塗装
(刷毛塗り)
刷毛塗りの場合は同じ色の物を揃えておき効率よく塗ります。新品の刷毛はそのまま使わず紙やすり等でしごいて毛先の形を整えたりしてなじむようにするのも有用です。
(塗らない選択もあり)
防舷材は実物はゴム製です。ABSの黒いフィラメントで造形後、ペーパーで仕上げるとゴム同様の質感が表現できますので塗装せずに使います。
7.4 組み立て
ある程度Assyがまとまったら、大きなパート(マスト、操舵室、キャビン、船体)ごとに組立てます。最終的には写真のように船体とキャビン、単独部品2つとなります。
① マスト
ABS樹脂の棒材を使って基軸にして、小部品の取付け穴や取付け位置のケガキ線を入れます。
各部品は接着する前に合わせ状態を確認し、ぴったり接着できるように形状の調整をしておきます。電線は這わせてから塗装します。(写真の黒い電線はダミーで、塗装後に取り付けています)
② 操舵室と天井の固定
天井にはマストの電装を含む電線を這わせてながら接着します。室内の器具や備品を床と壁に接着し、マストを取り付けた天井を接着します。(室内の床はねじで外せるようにしてあります)
③ キャビンと操舵室の固定
マストがついた操舵室は、キャビンの天井の裏からねじで固定します。あらかじめ取り付け穴をあけ、規定位置に置いて固定します。
④ キャビンの組立て
甲板(キャビンの天井)に、ベンチレター等の取り付け穴をあけて接着します。手すりは棒体の中心に0.5㎜のキリ(鉄鋼用ドリルの歯)を手作業であけ、真鍮かステンレスの0.5㎜線材に瞬間接着剤を付けて押し込み、2㎜程度出る位置でカットします。相手側も0.5㎜の穴をあけて接着剤でつないでいきます。
階段の手すりも同様につなげます。全部つなぎ終えたら甲板に置いて、現物合わせで取り付け穴をあけて接着します。
チェーンは手すり側に穴をあけ、線材を「J」型に加工してチェーンをひっかけたまま瞬間接着剤を付けて押し込んで固定します。
煙突は接着剤がはみ出るのを防ぐため、ピンで差し込むようにしています。
グースネックのベンチレターなど甲板から突き出た細いものは、甲板に穴をあけて通し、裏から接着すると取れにくくなります。
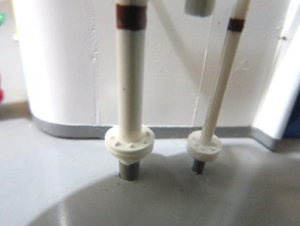
穴に通して裏で固定
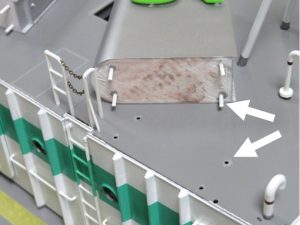
下部をピンにして固定
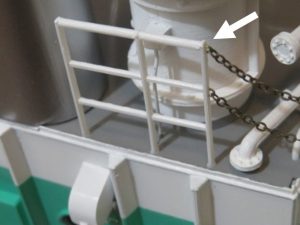
J形の線材で固定
⑤ 船体
ハル上部の端面はABSの板材を貼り合せたものをエポキシ接着剤で貼り付けます。
錨鎖は下部でつないで輪にして、手で回して錨鎖が動くようにしています。
防舷材は船体に小さい割ピンを接着し、水糸を墨で着色したもので結びます。あらかじめ
糸の位置にやすりで溝をつけておくと滑らず結びやすくなります。
後部ハッチ部分は脱着が必要なため、直上にあるガードは0.5㎜のピンで船体にはめ込むようにしています。
手すりの根元は前述のようにφ2に造形しているので、垂直にあけた穴に接着剤を付けて差し込みます
加工はここまでで終了です。
7.5 全体の組み立て
キャビン側の電装コネクタを船体側のコネクタに接続しながらキャビンを船体の上に載せ、単独の部品2つを組み立てれば完成です。
(電線は、航海灯、舷灯、外灯、操舵室、サーチライト、レーダ回転などをリモコン操作するため線の本数が多くなっています)
7.6 通電確認
組立時に船体側に電池をセットして点灯を確認します。
7.7 ウエイト調整
船体に駆動系のモータや架台、バッテリなどを想定される位置に置き、船体を水に浮かべてウエイトの重さと固定する位置を決めます。(子供用のビニールプールなどに浮かべる)ウエイトのブラケットも3Dプリンタで造形します。(船を動かさないときはウエイトは外しておきます)
【製作メモ4】工程あれこれ
◆旋回窓◆
窓内外に貼る部品、中央の部品を造形します。薄板ガラスを使いましたので、人工ダイヤのルータービットで時間をかけて穴をあけ、部品を接着します。ガラスに貼る部品はエポキシ接着剤を薄く塗って貼ります。
◆木の扉◆
造形した丸い窓枠の外径と内径と同じキリで、木に穴をあけ、かんなで厚め(0.3㎜程度)に削ります。内径用1枚、外径用は窓枠の厚み分木工用ボンドで貼合わせ、縁を貼り、乾いたら塗装します。(カシュー漆を6回塗り重ねています)
◆水密扉の開閉◆
3Dプリンタは角穴や細い溝の造形が得意なので、小さいドアヒンジを作り、開閉可能にしました。
ヒンジ1箇所につき角穴2つを開け、0.5㎜の溝を切ったプレートに、直角に曲げた0.5㎜の線材をはめて、角穴に通します。もう一方の角穴は、線材をはめないプレートを通して、ドアを閉じた状態で裏から接着します。
◆インレタの造形◆
船体の文字も3Dプリンタで造形し、インレタとして使います。0.5㎜厚程度の文字を造形したら、ベースから外さないで表面を平滑に仕上げ、塗装します。その後ベースから文字をはがし、裏側にエポキシ接着剤を薄く塗り、表面にマスキングテープを貼って所定の位置に貼り付けます。乾いてからマスキングテープをはがします。
8. 駆動系の実装
駆動系の構造や組み立ての詳細は割愛します。
推進器は市販品を取り付けます。推進器とモータの架台はアルミ板を加工しますが、リモコンのサーボやベヤリングのハウジングは現物に合わせて3Dプリンタで造形します。
強度が必要な箇所は一体で造形しないで2ピースにして接着します。
この後、バッテリをセットしてリモコンの設定と動作確認をすれば駆動系の組み立ては完了です。
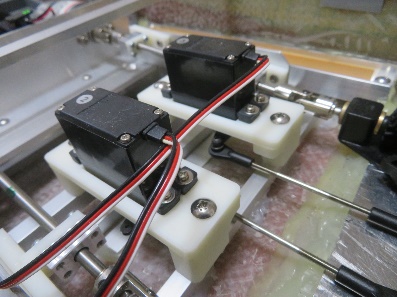
サーボのブラケット
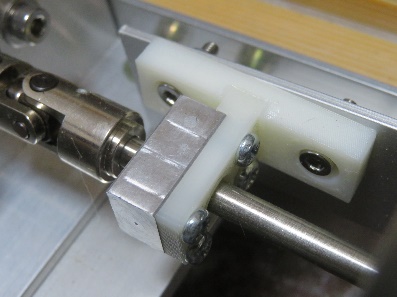
矢印部分で溝にはめこみ接着
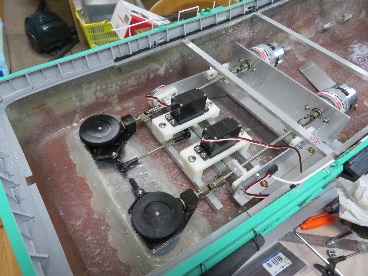
駆動系
9. 進水
船体にバッテリとウエイトをセットし、キャビンなどを船体に置いて、水の上に浮かべてリモコンを操作……うまく走りました。水に浮かべると本物っぽく見えます。
10. 製作を振り返って
実物の写真と比べても、満足できる仕上がりとなりました。
前述しましたが、曲線や曲面が多く、特に甲板とキャビンは幅方向が凸型、長手方向が凹型になっているため、CAD+3Dプリンタを使うことで正確な造形が実現しました。
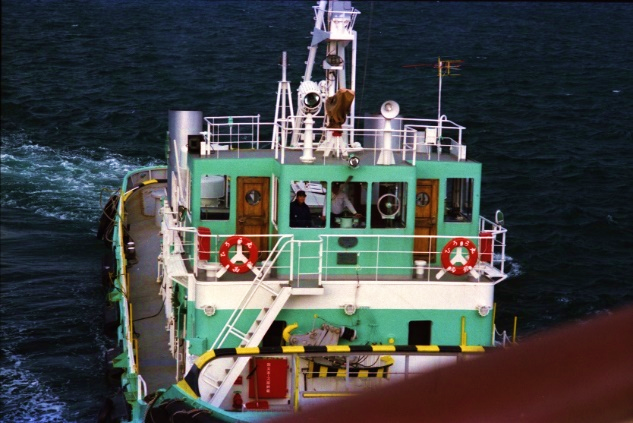
実物写真(ひうら丸)
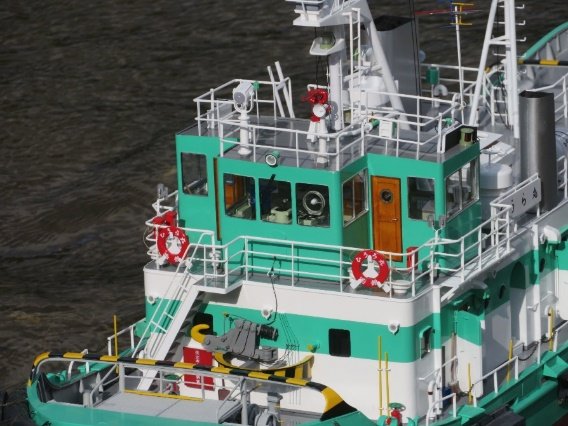
本模型
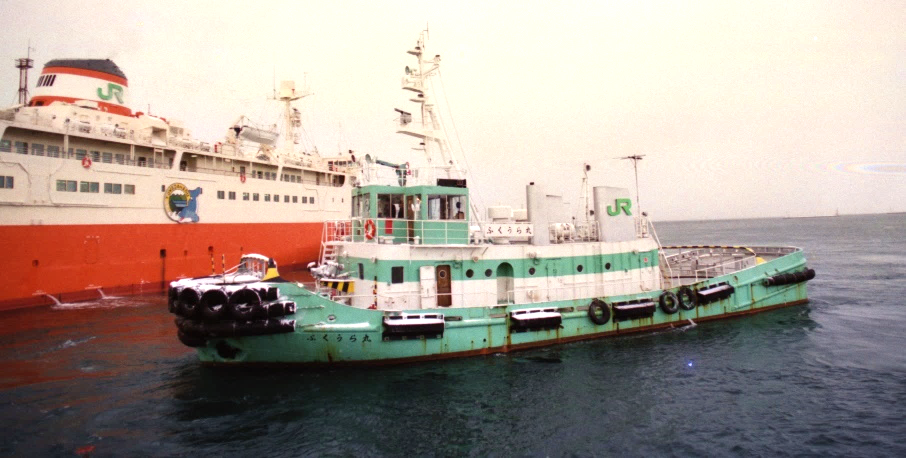
実物写真(同型船のふくうら丸)
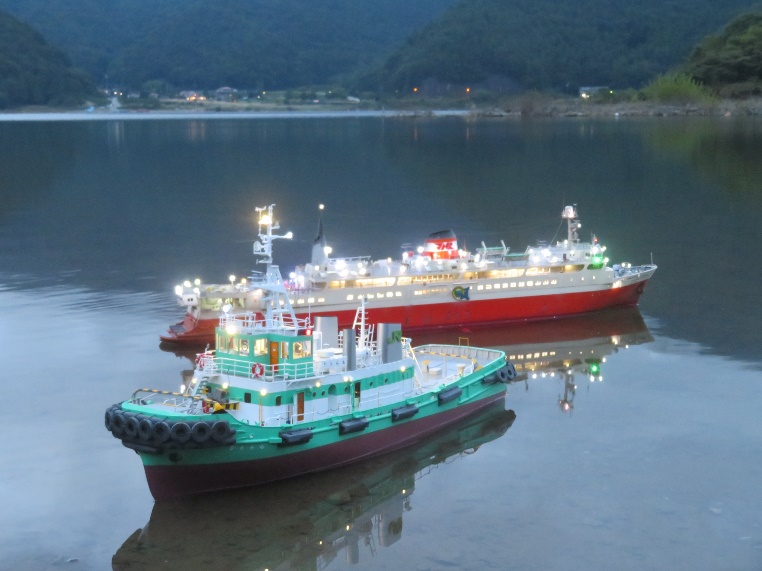
トワマさんの1/80十和田丸と 本模型
造形範囲が広いプリンタならハルの製作も可能になるでしょう。
3Dプリンタは…
・形状や造形の向きで最適なスライス設定を考えながら、造形が楽しめる
・手加工で簡単なものは3Dプリンタでは苦手、逆に手加工で困難なものは3Dプリン
タでは得意なので、不規則な面の合わせや曲面が多い船の部品は大活躍
・ほしい部品がすぐ自宅で作れる
など、とても魅力的なツールでした。
いままで作れなかったものも、3Dプリンタを使うことで模型製作の幅が広がります。
みなさんも是非挑戦してみてください。
平川地 まばせ
11.NSS編集後記
数年前にショールームに船舶模型の部品を作成する為に3Dプリンタとはどんな装置か知りたいとしたいとお越しいただいた方で、3DCADも未経験との事でした。
3Dプリンタをご導入頂き、3Dプリンタを活用した本格的な模型作り始まると、使用方法やトラブルのお問い合わせを頂き、対応させて頂いてるなかで模型作りの進捗写真をご共有頂き、クオリティの高さにぜひ弊社のWEBサイトで紹介させ頂きたいとお願いするに至りました。
記事の方も非常にマニアックでプロフェッショナルな内容を頂いておりますが、平川地まばせ さんのその探求心と努力には頭が下がります。
ここからは、船舶模型にご活用頂ける製品を少しご紹介させていただきます。
通常ABSやPLAなどをFDMタイプの3Dプリンターで造形すると、積層間にどうしても隙間が出来てしまい水漏れが発生してしまいます。
ですので、上記記事でも船体にはGFRPを木型で成型されておられました。
そこでポリプロピレンにグラスウール(ガラス繊維)を混ぜこんである「PPGWフィラメント」を使用してφ0.6mmノズルで0.15mm積層ピッチで造形すれば水漏れ(エアー漏れも)しませんので水漏れを嫌う箇所にご活用が可能です。
PPGWフィラメントは通常のフィラメントよりノズルが摩耗しやすいなど造形条件に癖もありますが、強度が欲しい、耐薬品性が求められる箇所にご活用頂けます。
下記に参考動画や弊社記事もございます。是非ご確認ください。
下記参考動画
また、光造形方式の3プリンタも最近安価になってきており、10万以下で購入が可能かつ十分使用に足りる性能の光造形3Dプリンタも増えてきています。
そういった光造形方式3Dプリンタを使用すれば、小さいパーツの更なる高クオリティでの造形が実現が可能です。
ご興味のある方は下記URLにて紹介させて頂きますのでそちらをご確認ください。
最後になりますが、数年にもおよぶ、平川地まばせ様の熱意と努力に改めて敬意を表させていただきます。
次回作を楽しみにしております。
■商品紹介URL
・PPGWフィラメントチラシ:https://nssngt.com/wp-content/uploads/2022/07/PPGW.pdf
・ガラス繊維強化フィラメント(PPGWフィラメント)の造形方法:https://nssngt.com/2019/06/13/975/
・日本製アレルギーフリー水洗いレジン「エキマテ」商品ページリンク:エキマテ
・3Dプリンタ用水洗いレジンを直接下水道に流す為に事前確認するべき事:https://nssngt.com/2022/08/09/2536/